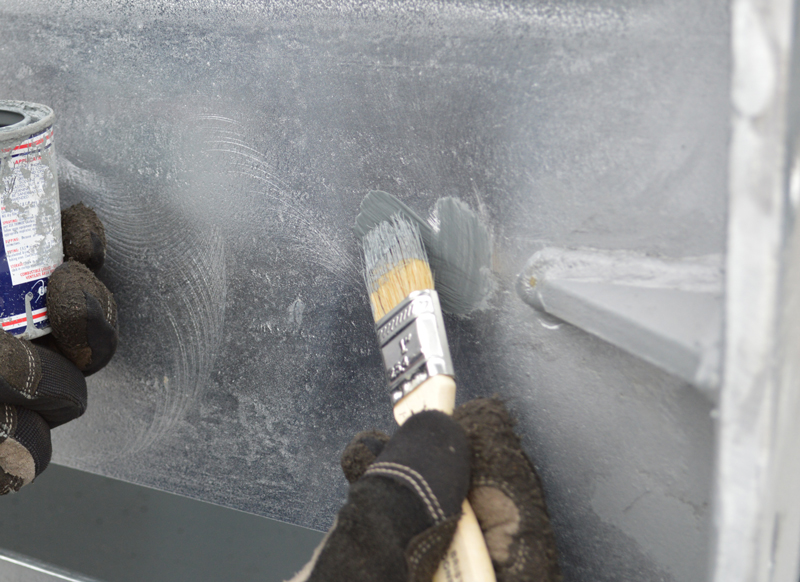
These primers can be either zinc rich or reduced zinc types. Steel Structural Supports with a 3-Coat Paint System.
Steel Structural Supports with a 3-Coat Paint System.
In a 3 coat system which coat normally uses zinc. A 3-coat paint system consists of a primary coat an intermediate coat and a top coat of a color or finish typically specified by the end user. View some of our products manufactured with a three coat paint system. Steel Structural Supports with a 3-Coat Paint System.
A very common zinc coating technology is electrolytic deposition of a zinc coating from an electrolyte 14. In this system a zinc electrode anode is connected to the positive pole of a source of direct electric current Figure 11. Zinc ions contained in the electrolyte are deposited on the negative cathode represented by the steel product.
Aluminum nickel and bismuth which help with zinc fluidity and consumption coating appearance etc. While in the galvanizing kettle the molten zinc metallurgically reacts with the iron in the steel to form the coating. After removal from the zinc bath the coating is inspected for conformance to.
E-coating refers to electrophoretic painting or electrocoating a metal coating technology developed to apply anti-corrosive coating. The e-coating process involves immersing the part in a series of dip tanks first to pre-treat and apply zinc phosphate and then to coat clean rinse and condition it. Zincsexcellent corrosion resistance in most environments accounts for its successful use as a protective coating on a variety of products and in many exposure conditions.
This proven corrosion resistance is a result of zincs ability to form dense adherent corrosion byproducts which leads to a rate of corrosion considerably lower than ferrous materials 10 to 100 times slower depending on the. Polyurethane Polyurethane paints are usually applied as a finish coat on the zinc primer or epoxy Figure 1. Several types of polyurethane paints can also be applied directly to steel without the use of primers.
These finishes which are characterized by their color retention and gloss are generally not required for interior environments. Zinc powder coating is an anti-corrosive primer designed to protect steel substrates. Used in a two-coat system zinc powder coating forms a resilient base layer.
For exterior use you will need to then apply a second layer which will be a polyester powder coating. Zinc powder coating has these main benefits. Resistance to corrosion and chemicals.
Often times the coating system starts with either an epoxy or zinc rich coating as the primer an intermediate coat of epoxy and a finish coat of epoxy or polyurethane. One of the main reasons multiple coat systems are used is because certain materials do an excellent in one aspect of corrosion protection but not so well in others. Zinc phosphate epoxy primers are the most frequently encountered and give the best durability within the group.
These primers can be either zinc rich or reduced zinc types. Zinc rich primers produce films which contain about 85 by weight of metallic zinc powder and the reduced zinc type as low as 55 by weight. System 3 A2 Inorganic zinc75 microns Epoxy polyamide25 microns Epoxy polyamide125 microns Fluorocarbon topcoat30 microns System 4 CMa Intermediate epoxy200 microns Epoxy acrylic topcoat75 microns System 5 CMp Intermediate epoxy200.
Electrophoretic deposition EPD is a term for a broad range of industrial processes which includes electrocoating cathodic electrodeposition anodic electrodeposition and electrophoretic coating or electrophoretic paintingA characteristic feature of this process is that colloidal particles suspended in a liquid medium migrate under the influence of an electric field electrophoresis and. Allied uses special high-grade quality zinc for its galvanizing operation. Our zinc is 9999 pure and contains only a trace amount of lead.
Hot-dipped galvanized pipe or pipe made from pre-galvanized steel coils normally use Prime Western grade zinc and other grades which contain a high level of lead sometimes more than 1. Iron phosphate pretreatment is the most common pretreatment for powder coating because it can be used with almost any material and has more environmentally friendly by-products or sludge. This process is commonly used on steel materials.
Zinc phosphate is a non-metallic crystalline coating that is extremely adherent to materials. Parts or components to be coated are generally transferred to a conveyor which is part of the coating system. Steel is the most common metal to be electrocoated.
For optimum corrosion protection and overall paint performance the recommended pretreatment for steel is the zinc phosphate system. Series 90G-1K97 Tneme-Zinc. Uses Primer andor Block Fillers.
Generic Description Aromatic Polyurethane Zinc-Rich. An advanced technology single-component moisture-cured zinc-rich primer providing extraordinary performance user-friendly and easy application. Also used for field touch-up of inorganic zinc coating.
As with other zinc coatings it should not be used outside a pH range of about 6 to 12. Nor should IZS be used for applications where it will be continually wet such as water tanks or underground. As a single-coat thin-film system it can provide great cost and time savings as blasting and coating can often be done in a day.
Use a hand grinder to remove excess zinc if any on a freshly galvanized surface. Cleaning in Alkaline Solution A 10 alkaline solution is used to remove oily and organic contaminants from the surface with minimum damage to zinc coating. If the solution is used in a pressure spray wash high pressure should not be used maximum 1400 psi.